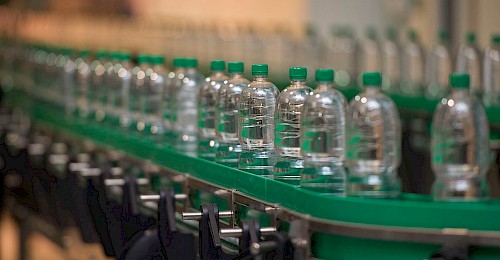
Infrared Heating in PET Manufacturing: Reducing Waste & Improving Productivity
Smarter, Greener, Faster: Why Infrared Heating is Transforming PET Manufacturing
Plastic production manufacturers are always looking for ways to improve energy efficiency, minimise waste and increase productivity. An impactful use of infrared heating is in PET manufacturing. As polyethylene terephthalate (PET) continues to be a staple in packaging, textiles, container industries and more, upgrading traditional heating methods provides a necessary competitive advantage.
Why PET Needs Infrared Precision Heating
PET (polyethylene terephthalate) is a highly versatile thermoplastic, but processing it requires precise temperature control. Overheating or uneven heating can lead to poor material quality, higher rejection rates and unnecessary energy consumption. Conventional heating methods, such as convection ovens or hot air systems, often fall short in achieving uniform temperature distribution, especially at high speeds or large scales. That’s where infrared heaters for plastic manufacturing come in.
These systems provide a targeted, rapid, and consistent heat source, which is ideal for shaping, moulding, and recycling PET products.
The Benefits of Infrared Heating in PET Processing
Energy Efficiency: Energy-efficient PET processing is important, both from a cost perspective and an environmental standpoint. Infrared heating delivers energy directly to the material’s surface through electromagnetic waves. This direct heat transfer is far more efficient than warming air or surrounding components first. As a result, manufacturers report energy savings of up to 40% compared to conventional heating systems.
Faster Processing Times: Speed is improtant in manufacturing. Infrared heaters can reach their operating temperature in seconds, significantly reducing start-up times. In PET thermoforming or preform heating applications, this speed translates to faster cycle times, improved throughput, and lower operating costs.
Improved Product Quality: Uniform heating maintains PET’s molecular structure for a consistent end product. Industrial infrared heating systems are designed to offer precise temperature control, reducing the risk of uneven heat distribution that can lead to defects or weak spots. This improves both quality and customer satisfaction.
Lower Waste & Scrap Rates: With better temperature control and reduced chances of overheating, infrared heating in PET manufacturing directly contributes to lower material waste. A consistent heating profile ensures fewer rejected parts and reduced scrap rates, for more sustainable and efficienty operations.
Applications in PET Manufacturing
Infrared technology has found its place in various stages of PET manufacturing:
- Perform Heating: Before blow moulding, PET performs must be heated uniformly. Infrared systems provide the speed and control needed for optimal stretch-blow results.
- Sheet Extrusion & Thermoforming: Infrared heaters ensure that PET sheets are evenly heated before forming, leading to better part consistency.
- Recycling Processes: In recycled PET (rPET) applications, infrared heating helps maintain material integrity while reducing energy input.
Customisable & Scalable Solutions
One of the advantages of modern industrial infrared heating systems is their adaptability. Systems can be tailored to your production line no matter the size of your operation and completed with zoned heating, automated temperature controls, and smart diagnostics. Additionally, their compact design allows easy integration into existing setups, minimising downtime during upgrades.
A Greener Future with Infrared
Sustainability is no longer a buzzword, it’s a business imperative. By embracing energy-efficient PET processing, manufacturers not only reduce their carbon footprint but also appeal to eco-conscious consumers and stakeholders.
Infrared heating plays a vital role in aligning PET production with global sustainability goals. With reduced energy use, lower emissions, and minimised waste, the technology is a win-win for both profits and the planet.
Why Infrared Heating Is the Smart Investment for PET Production
As industries strive for greater efficiency, precision and sustainability, infrared heating in PET manufacturing emerges as one of the leading solutions. From faster processing times to lower waste and improved product quality, it offers a powerful upgrade to traditional heating methods.
If you're looking to future-proof your production line, infrared heaters for plastic manufacturing might just be the smartest investment you can make. Contact us today for more information.